Integrating a personalized touchscreen into your projects and devices offers numerous benefits and countless opportunities to deliver an innovative and truly customized user experience.
By incorporating customization with your touchscreen products, it allows you the freedom to tailor the user experience to its precise needs. Whether you are designing a new oven, HMI, treadmill, control panel or portable device, having full design and manufacturing autonomy for your touchscreen interface ensures each product interaction is intuitive, seamless, and separates your product from the rest.
Customizing your interface gives you the liberty to design with limitless capabilities and functions, unlike standard off-the-shelf touchscreen solutions. Purchasing a “stock” touchscreen/interface often comes with various limitations in terms of size, resolution, features, and ability to “stay up to date” with the latest software upgrades your products may feature. Owning your design and building your own custom touchscreen assembly gives you complete control with your preferred size, shape, and product enhancements such as custom graphics, anti-glare (AG finish) or anti-reflective finishes (AR finish), internal and edge fabrication, component integration, IC chip manufacturer and model selection, as well as interface connection (USB, I2C, etc.) and so much more.
In addition to the already listed customizations, you have the flexibility and options of modifying the front of the touchscreen as below:
- Thickness – adjusting thickness of the front can impact the sensitivity and responsiveness of the touchscreens. For example: Thinner cover glass on a PCAP design may offer better touch sensitivity but may sacrifice durability, while thicker glass provides more durability but may reduce sensitivity.
- Surface Treatment – applying coatings or treatments to the front can enhance your touchscreens performance and durability. For example: Etched Antiglare glass (AG glass) on a PCAP design can reduce reflections and improve visibility, while Oleophobic coatings can repel fingerprints and smudges. Anti-reflective (AR) treatments can be helpful on the rear of the glass, when a design is not optically bonded.
- Custom Shapes and Sizes – depending on the design requirements, the front can be customized into various shapes and sizes to fit specific displays or enclosures.
- Tempering – tempering the glass (tempered glass) can improve its strength and resistance to impact, making it more suitable for rugged or industrial environments.
- Custom Printing – adding logos, designs, textures, or other graphics to the front of the touchscreen through printing can enhance branding and provide functional information to users.
- Integration of Sensors – sensors such as Ambient Light Sensors can be integrated into the design without affecting touchscreen functionality.
- Gasketing and Sealing – ensuring proper gasketing and sealing around the inner edges of the cover glass is important for ingress protection (IP ratings) and preventing moisture or dust from entering the device.
- Optically bonding – removing all internal air gaps from a touchscreen assembly (not just the touchscreen but the entire assembly including the LCD) can increase durability, reduce internal reflection, and mitigate risk of internal dust, debris, and condensation. This type of fully optically bonded design is one of the greatest benefits of designing and controlling a fully optically bonded custom touchscreen assembly.
Simply put, developing your own touchscreen design can lead to cost savings and much higher user satisfaction in the long run. While there are investments in its initial design, these investments give you the power to heighten branding visibility, provide an idealistic experience for your target user, and the satisfaction knowing that your design will stand out from the competition.
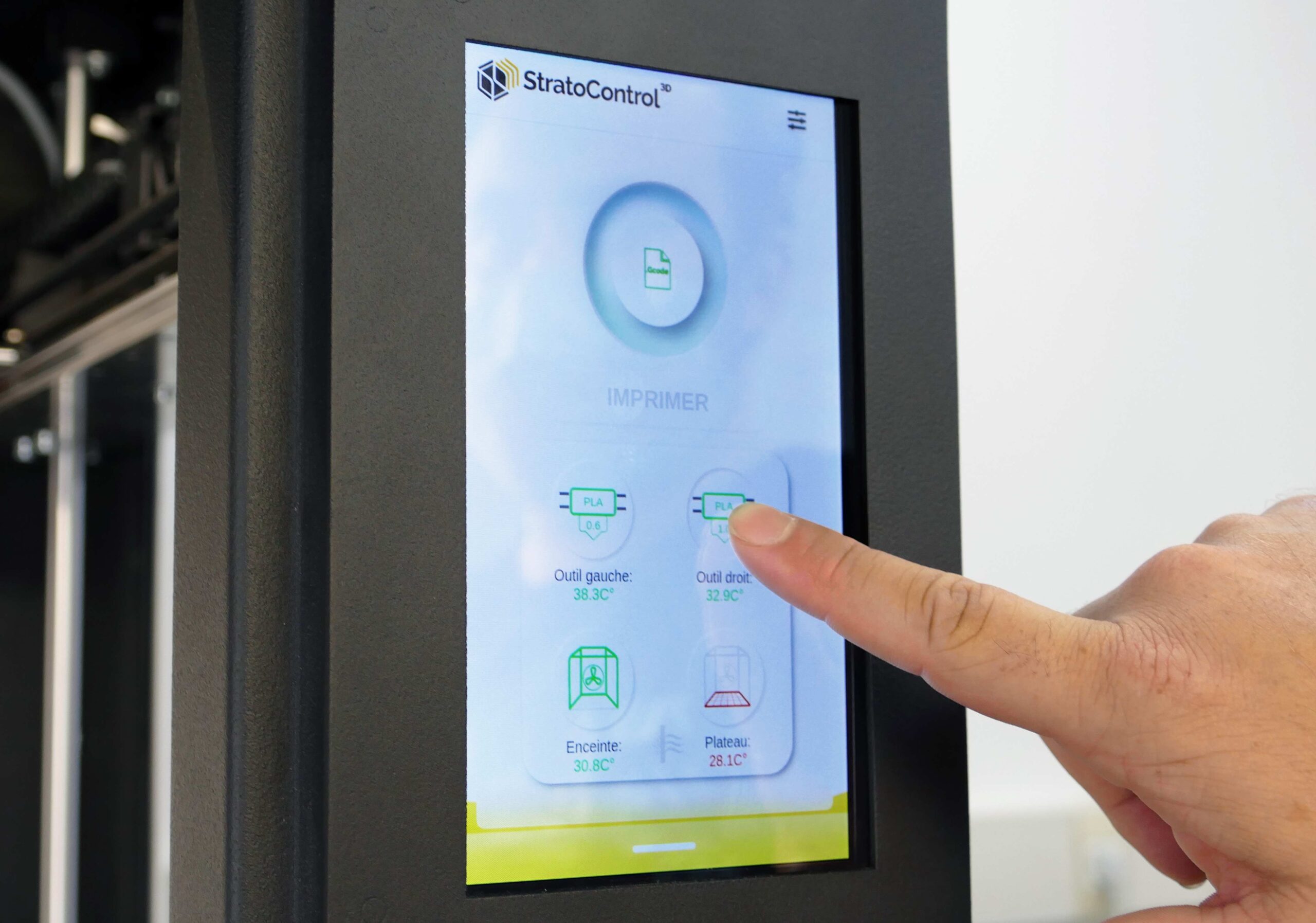